Category: Bez kategorii
Can Poland Utilize Natural Gas in the Automotive Sector?
Let’s start with a brief description of the state of Polish automotive industry: Poland is the most motorized country in Europe. Surprised? Let’s look at the data. By the end of 2022, there were 34.86 million motor vehicles registered in Poland (including passenger cars, trucks, and motorcycles). This ranks our country first in the European Union in terms of motorization rate (number of passenger cars per 1,000 residents) – 687, surpassing even wealthy Germany – 583. However, the average age of cars in Poland is over 14 years, while in Germany it is 10 years. Greeks and Estonians are bigger fans of old cars, with their vehicles averaging 17 years.
In the first part of the article, I described the actions taken by the European Union, along with our country’s government, to reduce the emission of greenhouse gases and toxic chemical compounds into the air. Consequently, the number of cars potentially subject to decommissioning could be enormous. If methane fuel has the potential to help us save nearly a 20-million fleet of old cars from scrapping, let’s take a closer look at it.
Let’s start with the fact that
Methane – a long-known fuel
The use of methane in the form of natural gas in automotive is not new. Already in the 1930s, this type of drive was widely used in England, Russia, and Italy. In Poland, several natural gas refueling stations were built in the 1950s. They were located in Rzeszów, Tarnów, Mysłowice, and Krosno. At that time, about 4,000 so-called technical cars were driven around Poland. The 1960s and 70s saw a complete regression in this field. Again, the first CNG refueling station was opened in 1988 at the Przemyśl-West natural gas mine. Since then, CNG fueling has been used in isolated cases of institutional transport vehicles, such as city bus transport. Currently, there are 56 CNG refueling stations in Poland, with 140 points (data as of January 2024).
For those new to this area, let’s start by explaining the concepts, i.e.,
How do CNG, LNG, and LPG differ?
CNG (Compressed Natural Gas) consists of 97% methane, compressed to a pressure of 20–25 MPa. Its octane number is 110–120. The processing does not require refining, only drying and filtering.
LNG (Liquefied Natural Gas) is natural gas that has been cooled to a temperature below -162°C. By changing to a liquid state, its volume is reduced by 630 times. It is mainly used in long-distance road transport, including for powering buses in urban transport. It is also used as fuel for barges and ships in inland and maritime transport.
LPG (Liquefied Petroleum Gas) is a mixture of propane and butane gases, compressed to 2 MPa. It is obtained as a byproduct during petroleum refining. The octane number of LPG is up to 130. Gasoline is needed to start the engine, and after reaching the proper operating temperature, it switches to gas fuel.
Let’s move on to specifics and look at the benefits of using methane fuel compared to petroleum-based fuels.
PROS
|
CONS |
ECOLOGY
|
Reduced exhaust pollution, 20% less CO2 emissions |
|
Zero emission of complex hydrocarbons (THC) |
|
Reduced CO emissions |
|
40% NOx emissions for compression ignition engines |
|
Zero emission of particulate matter (PM) |
|
Mitigation of the greenhouse effect |
|
Utilization of methane leaking into the atmosphere (from mines, fermenters) |
|
Bridges to high-pressure technologies – hydrogen |
|
Natural raw material, requires only filtering, no refining needed |
|
AVAILABILITY OF NATURAL GAS – METHANE
|
Good availability and broad diversification of sources compared to oil. Domestic reserves documented at 145 billion m3 |
|
Baltic Pipe gas pipeline from Norwegian fields through Denmark – with a capacity of 10 billion m3 per year |
|
From coal deposits 1-2 billion m3/year, resources 90 billion m3 |
|
From biomass composting |
|
From the gas terminal – 6.2 billion m3 currently, 7.5 billion m3 after expansion |
|
|
From the Yamal pipeline – 10 billion m3/year (total capacity 33 billion m3/year), currently suspended due to political reasons |
SAFETY
|
|
Requires storage under high pressure, 22 MPa |
Lighter than air, does not accumulate in depressions |
|
Auto-ignition temperature 595°C (diesel 240°C, gasoline 340°C) |
|
USAGE
|
|
Requires additional control of installations |
|
Cylindrical tanks take up additional space |
|
High own weight of steel tanks |
|
Or high price of composite tanks |
|
Longer refueling time, higher storage pressure of 30 MPa |
|
Limited number of CNG fuel stations, 56 stations with 140 points |
|
Vehicle range is 50% less than when fueled by diesel |
Does not require transport to fuel station, only connection to pipeline |
|
Possibility of self-refueling from home gas network |
|
EXPLOITATION
|
Engine operation is about 10 dB quieter |
|
Less knocking combustion, octane number 110-120 |
|
Simpler engine construction |
|
Highest energy value 48 MJ/kg |
|
Suitable for use in spark ignition (SI) gasoline and compression ignition (CI) diesel engines with no significant modifications |
|
The above summary of the benefits of using CNG is undeniable. If it is so good, then why do so few of us drive on CNG? Research by the author shows that the factor discouraging potential Polish customers from using this fuel is primarily the limited availability of refueling stations. However, let us recall the experiences associated with the introduction of LPG to the market. Initially, in the 1990s, there were only a few dozen stations across Poland, but today LPG is available at most gas stations.”
This translation presents the situation and potential obstacles for adopting CNG in Poland, drawing parallels with the historical context of LPG adoption.
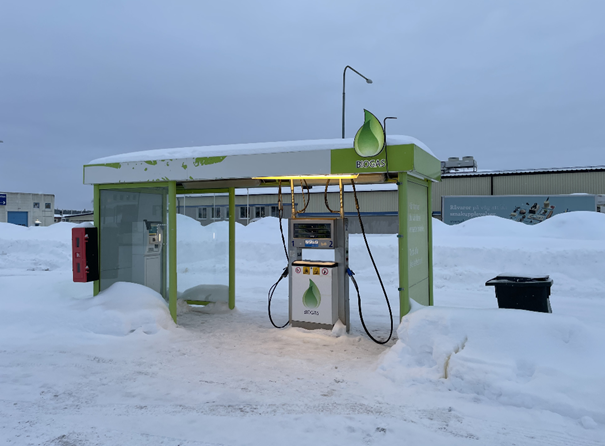
CNG self-refueling station in northern Sweden (photo: A. Górniak)
Author: Dr. Adam Górniak – long-time manager in the automotive industry, trainer, and consultant
List of sources:
What is a 3D scanner?
3D scanners, also known as Optical Measurement Machines, are the foundation of modern measurement techniques, enabling the touchless collection of accurate geometric data of objects. These devices are widely used in engineering, manufacturing, entertainment, and the protection of cultural heritage, offering precise digital replicas of physical objects. They allow for reverse engineering, prototyping, and quality control, speeding up production and design processes by quickly gathering large amounts of information with high accuracy, often up to 0.02 mm.
3D scanning transforms objects into digital models, primarily in the STL format, used in quality control, CAD design, and entertainment, such as special effects in movies. Their versatility and mobility allow for easy movement and measurement in different locations, even those hard to reach, making 3D scanners an indispensable tool in many situations. Optical and laser technologies used in scanning have specific applications and limitations but offer solutions even for surfaces difficult to scan, such as transparent or shiny ones.
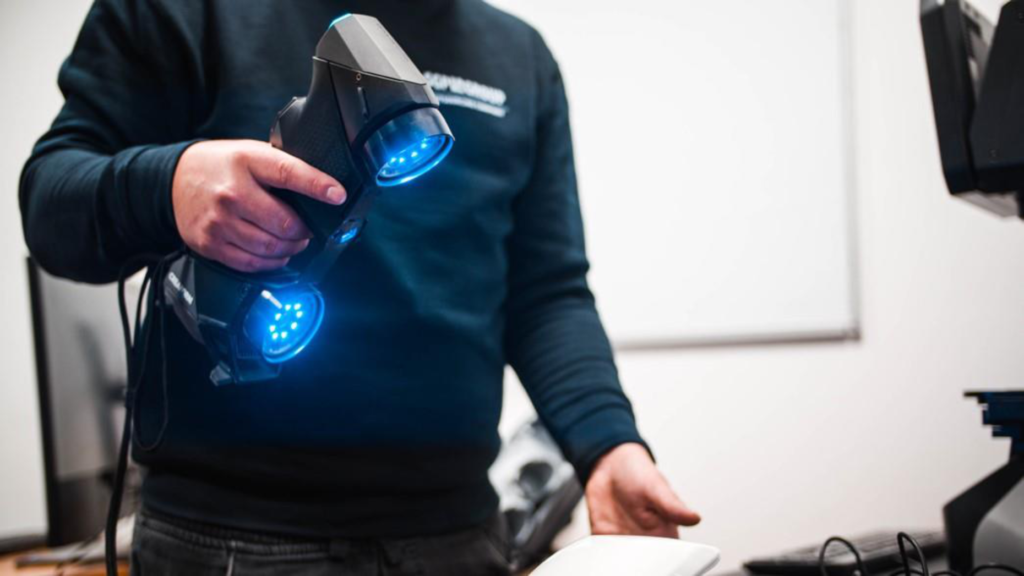
Our technologist during detail scanning.
Data from 3D scanners are used in the production of films and games, industrial design, orthotic production, prototyping, quality control, reverse engineering, and in medicine for creating personalized implants and prostheses. They are also invaluable in the documentation and conservation of cultural objects, contributing to their protection for future generations.
Types and technologies of 3D scanners
3D scanners are advanced devices used for digitizing spatial forms of objects, transforming them into accurate digital models. Their operation is based on complex technologies that enable precise capturing of data about the geometry of scanned objects. Below are the main types of 3D scanners and the technologies they are based on.
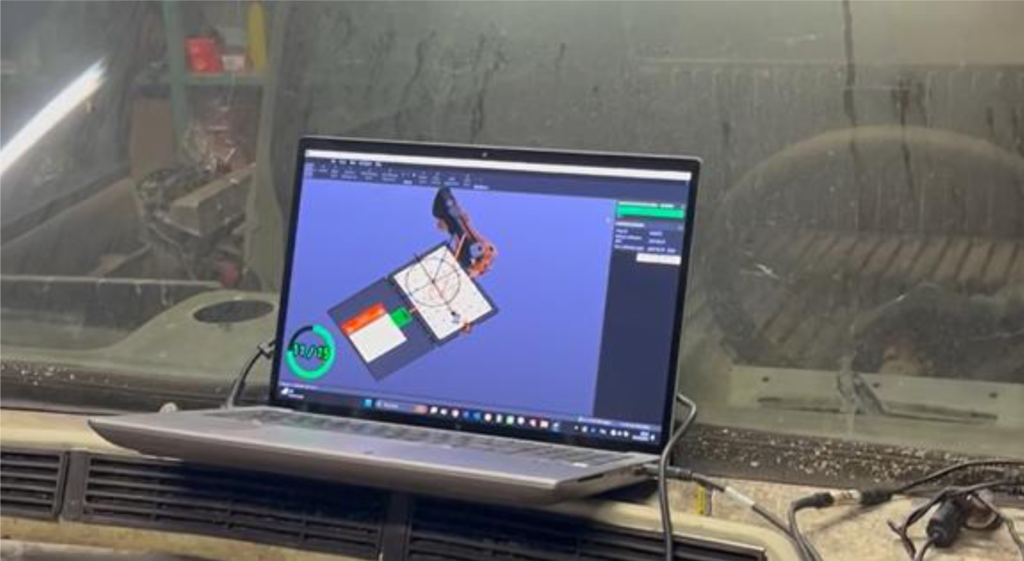
3D Scanner Calibration Process
1.Structured Light Scanners
These scanners use LED projectors to emit light patterns onto the object being scanned and then track the changes in these patterns caused by the object’s topography using two cameras. They are extremely precise, though they require static working conditions, meaning neither the scanned object nor the measuring head can move during scanning. Despite some limitations in mobility, structured light scanners offer high measurement accuracy, which is crucial in many industrial and research applications.
2.Laser Scanners
Laser scanners operate by projecting a laser onto the scanned object and analyzing the deformation of the laser stripes by two cameras. This allows for dynamic generation of measurement data, which facilitates the scanning of moving objects and increases the system’s mobility. Laser scanners, especially handheld ones, are more flexible in use and can operate in difficult conditions, including confined spaces and industrial environments with vibrations.
3D Scanner Technologies
Contact scanners require physical touch with the object, which can be a limitation in the case of delicate or intricate details. However, they are irreplaceable in precisely measuring dimensions and can be used in applications where the highest accuracy is required.
These scanners emit various types of radiation (light, ultrasound, X-rays) and analyze its reflection or penetration through the object. They can be divided into:
- Structured Light: Use light to project patterns onto the object and analyze the deformations of these patterns. They are fast and precise, ideal for scanning large areas.
- Laser Light: Emit laser light onto the object and record the deformations. They are exceptionally accurate, especially for objects with complex geometries.
These scanners rely on the detection of natural or illumination light reflected from the scanned object. They do not require emitting their own radiation, making them less invasive. They are relatively cheap to produce and can be used in various applications where less measurement accuracy is sufficient.
The choice of the appropriate type and technology of 3D scanner depends on the specific requirements of the application, such as accuracy, speed, mobility, and environmental conditions. Structured light scanners offer high precision in controlled conditions, while laser scanners provide greater flexibility and mobility in the field. Contact technologies remain indispensable in some engineering applications where maximum precision is required. Meanwhile, non-contact technologies, both active and passive, represent a wide range of tools tailored to various measurement needs, from documenting cultural heritage to comprehensive engineering and design analyses.
3D Scanner Operating Principle
One of the key methods used in 3D scanning is the technique based on the Moiré fringe distortion effect. Below, the process is detailed along with the technologies and methods used to obtain accurate digital replicas of objects.
Use of the Moiré Fringe Distortion Effect
- Fundamentals of the Effect: The Moiré fringe distortion effect is based on the projection of a line pattern (raster) with a known density onto the surface of the scanned object. This pattern distorts in a way that depends on the geometry of the object, allowing for an accurate representation of its shape in three dimensions.
- Capturing the Distortions: Precision digital cameras are used to capture the distorted pattern. These cameras register changes in grayscale between the lines of the pattern and the object’s surface, which allows for precise determination of the points’ positions on the surface of the scanned item.
- Creating a Point Cloud: The information obtained by the cameras is converted into digital coordinates, creating what is known as a point cloud. Each point in the cloud represents a specific place on the object’s surface, which after processing, allows for the reconstruction of its three-dimensional model.
Use of Reference Points
- Role of Reference Points: To ensure the stability and precision of the point cloud, reference points are used. They can be placed directly on the object or in its surroundings. Thanks to these markers, the scanning system can accurately navigate in space, allowing for precise placement of the measurement data in the global coordinate system.
- Markerless Tracking Systems: Some systems use external tracking devices, which eliminate the need for reference points. This allows for maintaining high measurement accuracy without the need to physically mark the scanned object.
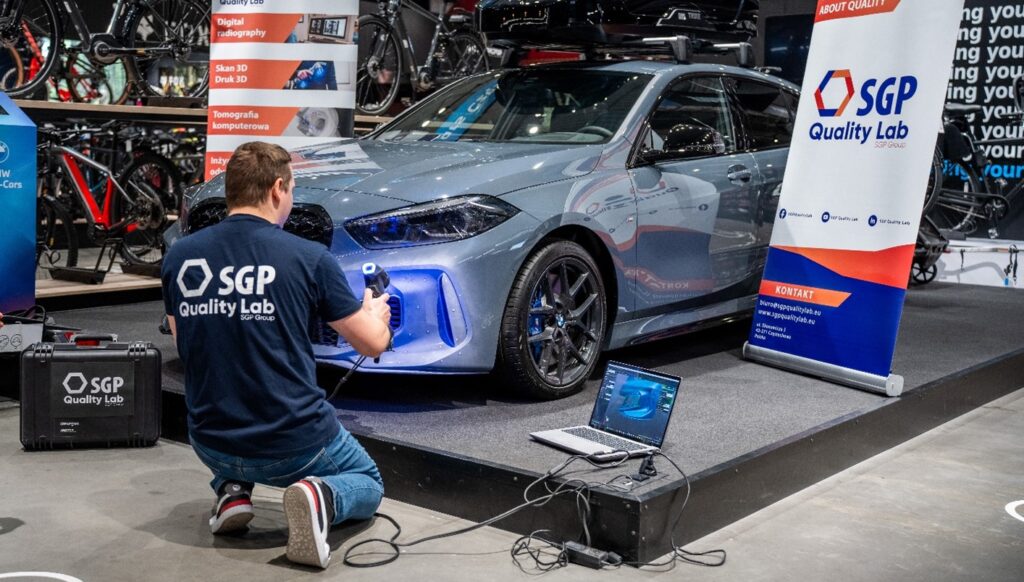
Laser stripe distortions on a car bumper and direct view of the scanned detail
Data Integration and Model Creation
- Combining Scans: For scanning larger or more complicated objects, individual scans must be integrated with each other. This process can utilize geometric features or color details to accurately match different parts of the scan into a coherent 3D model.
- Processing and Optimization: After compiling all the data, software processes and optimizes the model, removing any inconsistencies and improving the quality of the final digital object. In this way, an accurate and detailed replica of the scanned item is obtained, ready for further use in various applications.
Generated Data and Postprocessing in 3D Scanners
3D scanning starts with digitization, the precise capture of an object’s geometry, and ends with postprocessing, which transforms raw data into useful models. Below, both of these phases are detailed.
Phase 1: Data Generation by 3D Scanning
- Digitization of Geometry: The process begins with moving the measuring head along the entire geometry of the scanned object. The goal is to capture all surfaces of the object to analyze them accurately. The key aspect here is precision, enabling the system to recognize even the smallest details.
- Impact of External Factors: The accuracy of 3D scanning can be hindered by various difficult-to-control external factors, such as changes in temperature, shocks, external light sources, the type of material of the object, or reflections. These factors can cause information about the same surface to be recorded by the system as many different points.
- Raw Point Clouds: The result of scanning is what is known as a raw point cloud, a collection of all the point coordinates captured by the measuring system. This is a preliminary form of data that requires further processing to become a useful model.
Phase 2: Postprocessing and Polygonization
- Polygonization Process: There is an automatic optimization and averaging of raw data to transform it into a uniform and precise STL triangle mesh. Polygonization is a key stage of postprocessing, where points are connected into planes, creating a simplified representation of the object’s geometry in the form of a mesh.
- Utility of the STL Mesh: The resulting STL triangle mesh is a format that can be used in many applications, such as quality control of products, reverse engineering, computer simulations, 3D printing, and visualizations. It is a format widely accepted by CAD, CAM, and other engineering and design tools.
- Further Analysis and Applications: The STL model can then be used for detailed analyses, including checking conformity with original design specifications, simulating the behavior of components under various conditions, or for creating prototypes and final products. Data generation and postprocessing in 3D scanners are processes that together form the foundation for accurately replicating physical objects in a digital environment. Starting from a raw point cloud and ending with detailed 3D models, 3D scanning enables the transformation of physical reality into digital data, which can then be analyzed, modified, and used in a wide range of industrial and scientific applications.
Examples of 3D Scanners
Usage Thanks to their versatility and ability to accurately reproduce shapes in three-dimensional space, 3D scanning has found wide application across various industry sectors and fields of life. Below, we detail how 3D scanners are used in different industries and the benefits they bring.
- Castings, Forgings, and Molds: 3D scanning enables precise quality control and dimension verification of castings and forgings, which is essential in many manufacturing processes.
- Plastic and Composite Components: 3D scanning allows for the precise analysis and design of components made of plastics and carbon fiber, which is crucial for industries such as aviation and automotive.
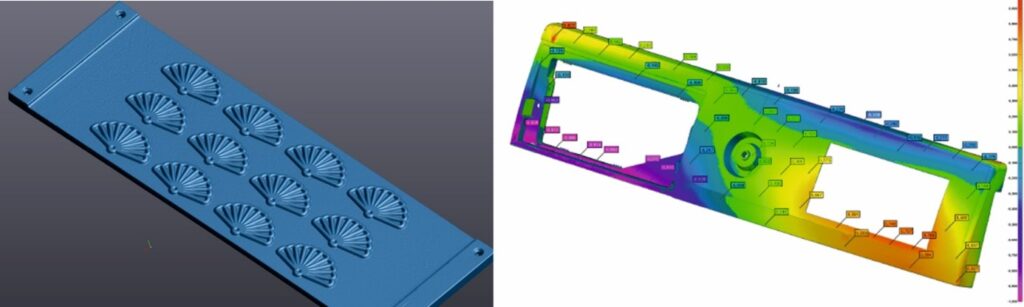
Mesh grid of the replicated detail (on the left) and rainbow analysis – gradient of deviations from the nominal (on the right)
- Automotive Parts and Bodyworks: Scanning facilitates accurate fitting and designing of spare parts and optimization of bodywork design.
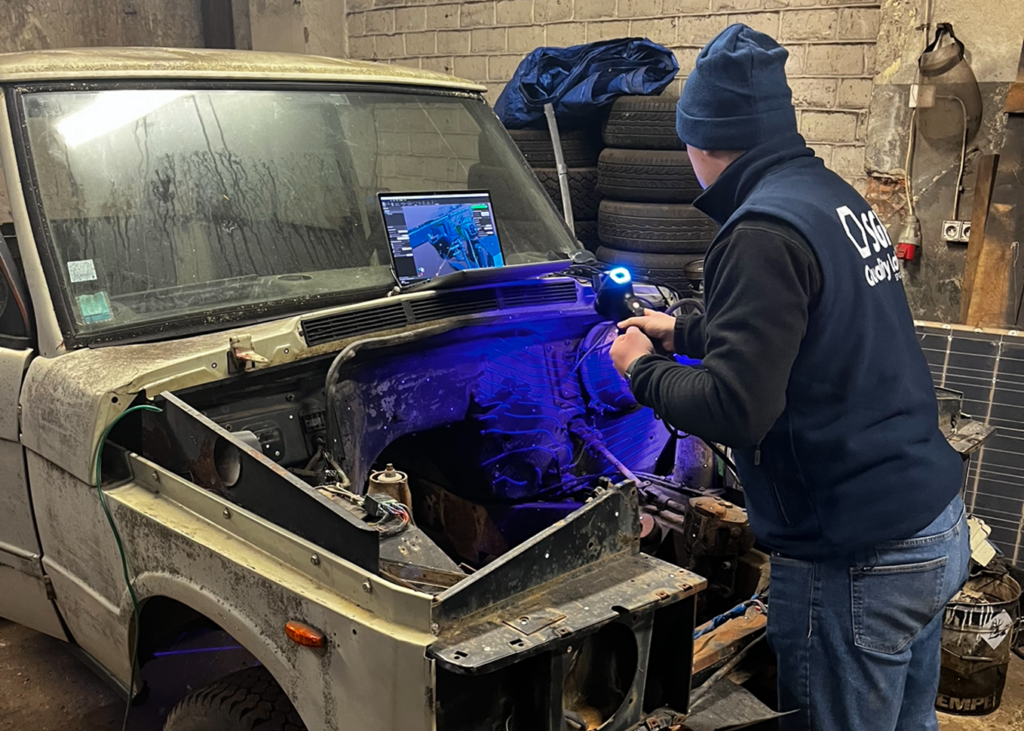
Our technologist during the scanning of the frame of an old Land Rover engine
- Boat Hulls and Yacht Cabins: In shipyards, 3D scanning accelerates the design and production process, enabling the creation of accurate models of hulls and cabins.
- Implants and Prostheses: In medicine, 3D scanners allow for the creation of personalized solutions that perfectly fit the needs of patients.
- Steel Structures and Welded Assemblies: 3D scanning is used to monitor the quality and accuracy of steel constructions, which is essential for safety and durability.
- Monuments and Artworks: In cultural heritage, 3D scanning enables documentation and protection of valuable artifacts and allows for the creation of accurate replicas for educational and exhibition purposes.
Summary
The high measurement accuracy, mobility, and versatility have made 3D scanners widely used in practically all types of industry around the world. Thanks to the amount of data generated in the 3D scanning process, we can obtain much more information about the quality of the produced product and detect its potential defects where we might not even expect them. Additionally, we gain the ability to recreate and optimize elements for which we do not have documentation or a CAD model, which can significantly impact the time it takes to design new parts.
If you have parts requiring digitization or are interested in professional services related to 3D scanning, please contact our consultant at bartlomiej.szybecki@sgpgroup. We also offer complimentary trial measurements and live demonstrations. You are also invited to our YouTube channel scanning 3D where we perform scanning of bicycle and automotive parts.
The Importance of Electronics in Cars
Contemporary cars are technologically complex machines in which advanced electronics play a crucial role, underscoring their necessity across a broad spectrum of applications. From engine management systems, through advanced traction control systems, to innovative electronic braking mechanisms – each of these elements utilizes digital technology to enhance safety, efficiency, and driving comfort. Additionally, advanced infotainment systems transform vehicles into mobile communication centers, offering passengers not only entertainment through access to multimedia and the Internet but also providing key navigational and telematic information, making them an integral part of modern mobility.
Furthermore, modern cars use between 1000 to 1400 semiconductor circuits, indicating their complexity and high degree of technological advancement. These circuits are scattered throughout the vehicle, from engine management systems, through safety systems, to comfort and entertainment modules. Their presence emphasizes the evolution of cars from mechanical structures to intelligent machines capable of making autonomous decisions based on data from multiple sensors and systems.
The cost of all the electronic equipment in a new passenger car often exceeds 40% of the vehicle’s value, which not only testifies to the importance of electronics for contemporary automotive but also its impact on production costs, final price for consumers, and on the overall design and functionality of the vehicle. This growing dependency on electronics also highlights the importance of continuous research and development in the field of automotive electronics, to ensure the highest levels of safety, energy efficiency, and user comfort.
Therefore, the development and integration of advanced electronic systems in cars are not just a trend but a necessity that defines the direction of future innovations in the automotive industry. With them, it is possible not only to improve traditional vehicle functions but also to introduce entirely new possibilities, such as autonomous driving, remote vehicle control, or advanced driver assistance systems, opening new perspectives for the future of motoring.
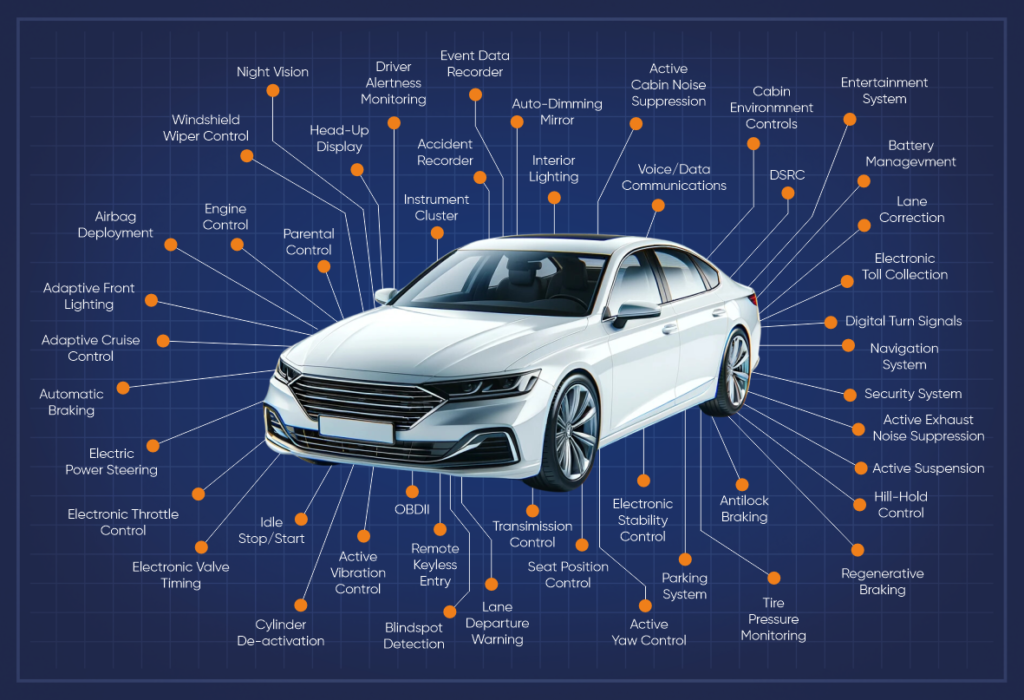
pic 1. Electronic systems in modern cars
The Use of X-Ray Technology in Quality Control of Automotive Electronics
The application of X-Ray technology in the quality control of automotive electronics components is a crucial element in maintaining high quality standards in the automotive industry. This advanced diagnostic method, allowing for the non-invasive examination of the internal structure of components, is invaluable for car manufacturers and suppliers in identifying and addressing potential problems early in the production or even design process.
X-Ray technology, also known as radiography in conjunction with computed tomography (CT), allows for detailed visualization of internal material structures without the need for physical disassembly or destruction. This method is particularly useful in the quality control of automotive electronics, including printed circuit boards (PCBs), microconnectors, wiring harnesses, and other key electronic components. It enables the detection of various defects, including:
- Micro-cracks and cracks in component casings, which can affect their durability and functionality.
- Soldering issues, such as cold solder joints or voids in soldered connections, which can weaken electrical conductivity and reliability of connections.
- Misplacements of electronic elements, which can lead to device malfunction.
- Shorts and breaks in conductive paths, crucial for the proper functioning of automotive electronics.
Technology and Inspection Methodology
The technology and inspection methodology based on the use of X-Ray radiation is a key element of modern control processes, especially in the context of electronic component analysis. This advanced inspection method allows for the penetration of objects using X-Ray radiation, which is absorbed to varying degrees by materials of different densities. This enables the creation of contrasted images of the internal structures of the component under examination, allowing for precise analysis of its condition and the identification of potential defects. With technological evolution, modern X-Ray inspection systems utilize both two-dimensional (2D) techniques and three-dimensional computed tomography (3D CT). Computed tomography is particularly valuable as it allows for the creation of detailed three-dimensional reconstructions of components’ internal structures.
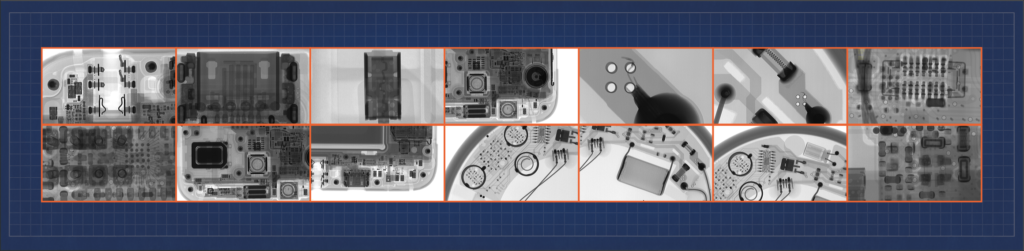
pic 2. Example realizations of electronic components
Benefits of Using X-Ray Technology
The implementation of X-Ray technology in inspection processes brings several benefits that significantly improve the quality and reliability of manufactured electronic components:
- Detection of Invisible Defects: X-Ray technology allows for the identification of defects that are invisible to traditional inspection methods, such as visual or manual checks.
- Increased Speed and Accuracy of Inspections: Thanks to the automation of image analysis processes, it is possible to significantly speed up control processes while simultaneously increasing their accuracy.
- Optimization of Production Processes: Rapid identification and elimination of defect causes allow for the optimization of production processes, reducing time and costs associated with quality control.
- Increased Reliability and Durability: By early detecting and eliminating potential defects, X-Ray technology contributes to increased reliability and durability of electronic components, which directly translates into the quality and safety of final products, including vehicles.
Conclusions
The integration of X-Ray technology in the automotive sector highlights the pursuit of excellence and is a strategic step for manufacturers in offering high-quality and reliable vehicles. It is key to building market position and gaining customer trust, leading to commercial success. Supporting this goal, SGP Quality Lab provides X-Ray inspection service for both individual orders and serial production, enabling effective quality control. Advanced technologies and the experience of SGP Quality Lab ensure accurate defect detection, raising the quality and competitiveness of products.
author: Łukasz Ciechowski – Quality and Development Manager
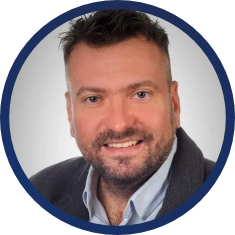
Can Poland use natural gas in automotive applications?
The 21st century began with the anticipated, or according to some, already observed greenhouse effect and worsening air pollution. The transport sector significantly contributes to these changes, primarily due to the emission of exhaust gases. However, in recent years, this has changed significantly. Thanks to advanced catalysts, efficient engines, start-stop systems, and additives for exhaust treatment such as AdBlue, cars emit significantly fewer exhaust gases and associated pollutants than they did just 10 years ago. Nevertheless, harmful substances for living organisms, especially in the exhaust of older vehicles, still exist in relatively high concentrations:
carbon monoxide (CO), hydrocarbons (HC) and their derivatives, often interchangeably referred to as volatile organic compounds (VOC), nitrogen oxides, sulfur oxides (oxide, dioxide, trioxide), lead and its compounds, soot, fumes, ashes, metals, other solid substances, heavy organic compounds in liquid form, partially interchangeably referred to as particulate matter PM.
Among substances harmless directly to the health of living organisms or occurring in exhaust gases in small concentrations are those harmful to the environment. They particularly contribute to the occurrence of the greenhouse effect in the atmosphere. These mainly include:
- carbon dioxide (CO2),
- methane (CH4),
- ammonia (NH3).
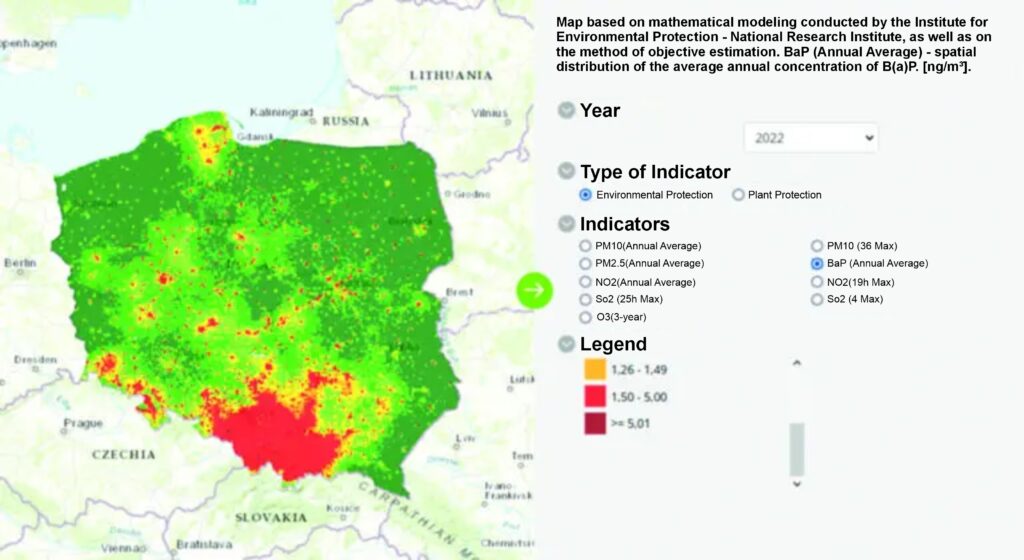
Pic. 1. https://powietrze.gios.gov.pl
To counteract the deterioration of air quality, the European Union is adopting increasingly stringent requirements regarding the cleanliness of car exhaust emissions. It’s enough to mention the Euro series standards, among which the latest edition – Euro 6d, introduced from 2021, obliges car manufacturers to ensure that the average carbon dioxide (CO2) emissions in their model range available in the European Union do not exceed 95 g/km. Slightly different values apply to brands offering smaller, mainly urban cars, and slightly higher values for those selling larger and heavier cars. It is important to note that for vehicles with diesel engines, the permissible emission of nitrogen oxides has been significantly reduced.
The need to comply with regulations in force in the European Union and concerns about air cleanliness, especially in city centers, led the Ministry of Climate and Environment to amend the law on electromobility and alternative fuels. It includes, among other things, the creation of clean transport zones in Poland. The first of these will be launched by mid-2024 in Warsaw and Krakow. Entry to the clean transport zones will be allowed for cars:
- electric,
- hydrogen-powered,
- natural gas-powered,
- exempted based on a municipal council resolution.
As a result, cars with diesel engines, as well as gasoline and LPG cars, will not be allowed to enter.
On the horizon is a group of several million owners of passenger and delivery vehicles equipped with engines that are several years old or older. These vehicles do not meet the requirements of Euro 4 and are increasingly unwelcome in large cities. In light of this, are we condemned to scrapping millions of passenger cars? I don’t think so. The only chance for their continued use is to switch to more environmentally friendly fuel. It can be a 50/50 solution, meaning vehicles with diesel engines are adapted to run on two fuels: diesel and natural gas in a 50%/50% proportion. This solution does not completely eliminate pollutants from exhaust emissions but significantly reduces them, allowing the continued use of existing fleets for several more years.

Pic. 2. www.pixabay.com
What can we do to drive more affordably and ecologically?
Methane as an Alternative to Petroleum Fuels
Internal combustion engines powered by petroleum fuels have dominated the automotive world for nearly 150 years. Current indications suggest that further improving engines for more efficient fuel combustion and cleaner emissions will become increasingly challenging and costly. This complexity involves advanced engine equipment, such as increasing fuel injection pressure (around 15 MPa for gasoline engines and 200 MPa for diesel engines), adjusting air intake, catalytic and filtering systems for exhaust gases, all interconnected with sophisticated computerized control. The detected falsification of emission quality analysis in Volkswagen vehicles in the United States is likely a signal that realistic improvements to internal combustion engines have reached their limits.
Since traditional internal combustion engines are reaching the end of their development, and mass adoption of electric cars is still a few years away, the question arises: what about the transitional period? The answer that comes to mind is natural gas.
Advantages of Natural Gas
Among the advantages of compressed natural gas (CNG), we can mention that:
It is environmentally friendly – significant reduction in pollutants emitted in exhaust gases, including:
-
- Solid particles PM 2.5 and PM 10 (so-called soot),
- Sulfur oxides (SOx),
- Nitrogen oxides (NOx),
- Carbon monoxide (CO).
- Noise reduction by several decibels due to high octane number – equivalent to approximately 130.
- Transportation of gas to refueling stations is possible through traditional gas pipelines, eliminating the need for fuel delivery by tankers (no pollution associated with transportation).
- Safety – the ability to park in garages and underground parking lots. CNG, being lighter than air, quickly dissipates into the atmosphere in case of a leak, for example, during an accident. When mixed with air, it forms non-flammable concentrations. The ignition temperature is higher than that of gasoline and diesel.
- No need for DPF/FAP filters (AdBlue) in vehicles – simpler construction and potential lower risk of costly engine and accessory failures.
- The possibility of refueling the car from a low-pressure home gas network using CNG compressors.
Will CNG remain one of the main sources of fuel in the long run? I do not know, as strategic decisions have already been made within the EU. However, from an economic and ecological standpoint, it is certainly worth considering methane gasification for the millions of vehicles currently on our roads. In the second part, I would like to delve into the Polish realities associated with CNG and explore the opinions of Polish drivers on this matter.
Author: Dr. Adam Górniak – long-time manager in the automotive industry, trainer, and consultant
The electric car has become synonymous with modern motoring for many of us. Is this really the case, or are there no other solutions? Published in April 2023, the Regulation of the European Parliament and of the Council (EU) 2023/851 […] regarding the strengthening of CO₂ emission standards for new passenger cars and for new light commercial vehicles, in practice forces manufacturers to stop producing so-called emission cars by 2035. So, what to do instead? Today, the obvious solution is an electric car. I won’t cover the issues related to such cars in this article, as they are quite well covered in the media. Here I want to focus on another, less well-known solution, which is a hydrogen-powered car.
Advantages and disadvantages
There are two technologies for automotive hydrogen propulsion: hydrogen combustion (ICE) and hydrogen electric cells (FCEV). Direct combustion of hydrogen in an internal combustion engine (on a similar basis to the combustion of natural gas, for example) is a technology that is still in the development stage, although trials of it have been going on for nearly 20 years. Currently, research into the hydrogenation of the internal combustion engine is being carried out by a number of automotive manufacturers such as Toyota, Ford, Deutz and the American Cummins. The latter has succeeded in modifying a 15-liter engine adapted to burn CNG – to hydrogen, without losing its efficiency. The second technology is the use of hydrogen cell energy in vehicles with electric engines.
Advantages of hydrogen cars:
- Long range (about 500 km on a single charge).
- Quick refueling (about 5 minutes).
- Zero-emission.
- Small batteries (using less lithium).
- Lighter overall vehicle weight (a full tank of hydrogen is only 5 kg).
Disadvantages of hydrogen cars:
- Low energy efficiency (estimated 38% compared to 73% for electric cars and 15-20% for combustion cars).
- Lack of infrastructure (one publicly available station in Poland, others in plans).
- Price of the car (about $78,000).
- Size of the car (must additionally accommodate electric cells).
- High cost of obtaining hydrogen.
It is worth noting that when Toyota Mirai is driven calmly, hydrogen consumption is in the range of 0.9 kg per 100 km. Considering the above data, when the price of 1 kg of hydrogen is $16.39, the cost of driving 650 km (one refueling) will be just over $95.
How it works.
Hydrogen cells are used to generate electricity and power an electric motor with it. Electricity is generated by a process we’ve known for more than 200 years, and that is the reverse electrolysis of water.
In the nutshell, it looks like this: you drive up to the refueling station under the dispenser (similar to how it works for LPG refueling) and fill the tank with hydrogen. Then:
- The hydrogen goes into the fuel cells.
- Hydrogen ions pass through a polymer membrane toward the anode.
- A reaction takes place in the cells, combining hydrogen ions (protons) at the anode with oxygen at the cathode.
- When hydrogen combines with oxygen from the air, water is formed.
The flow of electrons between the electrodes produces electricity, driving an electric motor and charging a battery.
Schematic of the construction of an alkaline fuel cell

1 – hydrogen, 2 – electron flow, 3 – charge (energy receiver), 4 – oxygen, 5 – cathode, 6 – electrolyte, 7 – anode, 8 – water, 9 – hydroxyl ions
To refuel, but where?
Hydrogen cars available on the Polish market are Toyota Mirai II and Hyundai Nexo. Unfortunately, these are expensive cars – they cost about PLN 300,000. If we already decide to buy one, we will face another challenge – where to refuel?
The project of the Polish Hydrogen Strategy in Poland until 2025 assumes a budget of PLN 2 billion for the development of hydrogen infrastructure, with 32 stations to be built in major urban areas. This will allow hydrogen-powered cars to travel seamlessly throughout Poland.

According to the Ministry of Climate and Environment, the distribution of hydrogen refueling stations could look as follows (map). Thirty-four station locations, eight starting city hubs were taken into account, and the basic condition was that the permissible distance between refueling stations could not exceed 200 kilometers.
The first publicly accessible hydrogen refueling station in Poland was opened in September 2023 in Warsaw. It is owned by PAK-PCE, while Orlen will still make four stations available in 2023: in Krakow, Katowice, Poznań and Włocławek. Seven more are planned: in Walbrzych (by 2024), and in Bielsko-Biala, Gorzow Wielkopolski, Krakow, Pila and Warsaw by mid-2025. In addition to Orlen, investors in the station network also want to be:
- Przedsiębiorstwo Komunikacji Metropolitalnej (Silesia),
- PAK-PCE Stations H2,
- Polenergia Elektrociepłownia Nowa Sarzyna,
- Promet-Plast.
There are already 163 hydrogen stations operating in Europe, with another 46 under construction.
The European Automobile Manufacturers Association (ACEA), which brings together 14 of the largest manufacturers of cars, vans, trucks and buses, estimates that at least 300 hydrogen refueling stations should be built in Europe by 2025, and at least 1,000 by 2030. The proposed distribution of the stations can be found in the maps below.

The direction of change in the development of the automotive industry is clear, so it is worth considering whether to wait and choose a hydrocar instead of an electric.
Regardless of your decision, I wish you that we shift to zero-emission cars as soon as possible and take care of the environment together.
Author: Dr. Adam Górniak – long-time manager in the automotive industry, trainer and consultant
List of sources:
https://www.gov.pl/web/klimat/rozpoczely-sie-konsultacje-publiczne-projektu-polskiej-strategii-wodorowej
https://www.gov.pl/web/klimat/propozycja-rozmieszczania-ogolnodostepnej-infrastruktury-ladowania
https://www.toyota.pl/porady/silnik-wodorowy-fakty-mity
https://www.acea.auto/figure/interactive-map-truck-hydrogen-refuelling-stations-needed-in-europe-by-2025-and-2030-per-country/
https://ceenergynews.com/hydrogen/orlen-signs-eu-deal-for-new-hydrogen-stations-in-poland/
https://motofocus.pl/elektromobilnosc/108251/wodor-w-motoryzacji-mozliwosci-i-ograniczenia
https://www.cummins.com/engines/hydrogen
https://devil-cars.pl/blog/samochod-na-wodor-jak-dziala-ile-kosztuje
If you want to learn more about hydrogen propulsion or have decided to cooperate with us, please contact
contact us! Below you will find contact details of our expert:
Bartłomiej Szybecki
Key Account Manager
+48 884 311 422
bartlomiej.szybecki@sgpgroup.eu
What’s the difference between traditional and CNC machining?
Professional metalworking continues to use both CNC machine tools and traditional machines that require manual operation. Before making a choice, it is useful to know what capabilities are offered by one or the other technology and which solution will work for you.
The main difference between CNC and traditional machining
The main difference is based on the design of the machine. In traditional machining, the machine used is manually operated and requires the constant presence of a worker. His tasks include manually programming the machine and controlling the machining process.
A CNC machine, on the other hand, is equipped with built-in computer software, and a specially designed program is responsible for its operation. In this way, the machine basically carries out its operations independently and needs to be operated only from the control cockpit.
What is the biggest advantage of CNC technology over traditional machinery?
The elimination of the human factor from the production process allows for the automation of activities and the achievement of repeatable results. During traditional metalworking, the end result mainly depends on the knowledge and skills of the machine operator (e.g., a turner or miller). The person responsible for the operation must also meet specific requirements: in addition to technical knowledge and professional training, good motor coordination is also necessary. At the same time, the operator must efficiently operate the various mechanisms, and at the same time control the results obtained with measuring tools. Taking these factors into account, when it comes to the production of larger batches of products, it is difficult to achieve repeatability of parameters, and making even a small mistake can prove very costly – especially at a later stage of production.
The biggest advantage and thus the advantage of CNC over traditional machines is precisely the achievement of measurement stability and high repeatability. Regardless of the size of the batch, the result obtained is characterized by precision, without affecting the efficiency and speed of the production process itself.
Impact of implementing CNC machining in production processes
The work program of the CNC machine tool is based on a digital model developed in advance using CAD/CAM software. All information is entered into computer databases, so there is easy access to it all the time. This makes it easy to trace the production process and optimize it by eliminating weak points. What do we gain this way?
- Reduction of working time – the same tasks are performed in a much faster way, thanks to process optimization. In addition, machines can changeover automatically, which generates further time savings.
- Greater efficiency – the parts are made in less time, and what’s more, the machine works at a constant pace. In contrast, with a human, it is not possible to maintain productivity at the same level for a longer period of time.
- Cost reduction – in traditional metalworking, the final quality of the product depends mostly on the skill of the worker. Meanwhile, a human cannot maintain the same level of concentration at all times.
In our Quality Lab, we have a CNC machine tool – DN VC 510 – which, with its rotary tables, precision spindle, advanced cooling system and programming capabilities, has all the above advantages.
Does always implementing CNC mean a better choice?
CNC machining brings a number of benefits, mentioned earlier: process optimization, increased productivity, lower production costs. Streamlining the process makes it possible to realize even larger batches of products in a relatively short time, while maintaining the required final standards. Sometimes, however, implementing CNC technology can prove costly. In cases involving low-complexity components and with a low risk of error, the use of traditional machining can still prove to be a cost-effective solution. Traditional solutions also work well in situations where only one-off products are involved, or for making up the parts needed, especially if electronic documentation is lacking.
If you want to learn more about the use of CNC technology or decided to cooperate with us please contact us!
Bartłomiej Szybecki
Key Account Manager
+48 884 311 422
bartlomiej.szybecki@sgpgroup.eu
CNC (Computerized Numerical Control) technology’s development turned out to be yet another significant turning point in the history of industry. In the 1950s, computerized numerical control technology was developed, instantly revolutionizing production procedures. Mass production was all but impossible due to the limits of instruments like lathes, grinders, and milling machines that operated manually or semi-automatically. It was a solution that greatly constrained productivity and production scalability, mostly due to the enormous time and labor investment.
The role of CNC in increasing the efficiency and precision of mass production of automobiles
By eliminating the need for an operator to operate the machine, production efficiency has been greatly improved and streamlined. Previously, each machine had to be controlled by an employee, who was only able to produce a limited number of components. In addition, one always has to reckon with the fact that some components are rejected at the quality control stage as defective.
The advancing digital revolution has made it possible to program the machine to perform a sequence of the same movements as a human, only much faster. Not only are products being made in much less time, but the number of defective parts is being significantly reduced. Manufacturing precision is crucial when components are part of complex subassemblies.
The potential inherent in CNC has made the technology widely used in virtually every industry. Industries such as automotive or aerospace manufacturing are now hard to imagine without CNC machinery. In the automotive industry, the main use of CNC machines is in the production of such details as gears, camshafts, valves, axles or metal cylinder blocks, but not only that. CNC is also useful when there is a need for short lead times like manufacturing spare parts or prototype car parts.
A perfect example of increasing production efficiency is a case study that describes how Quality Lab helped one of its customers accelerate mass production of hard-to-reach parts.
Examples of CNC application in various manufacturing processes
The possibilities for the use of CNC machines are practically unlimited, so in the automotive industry this technology is used both in the production of drive components and for turning rims or punching body parts. The programmed machines are suitable for machining a variety of materials, including those mostly used in the automotive industry: steel, aluminum or cast iron. Examples of processes using CNC technology include:
Machining
Otherwise known as cavity machining. As a result of this process, excess material (surplus) is removed. Precision-controlled, very sharp knives or chisels are used for removal. The use of CNC allows the exact parameters of the design to be maintained.
Milling
CNC milling is one of the machining methods and involves machining a stationary workpiece with a milling machine. The milling machine blades, moving in a rotary motion, gradually cut the top layer of the workpiece.
Drilling
Taking advantage of CNC technology makes it possible to make any holes according to a designated design. This includes, for example, drilling an even hole of a specified diameter and depth, countersinking, i.e. enlarging an existing hole, chamfering a hole for a screw head or threading.
Advantages of automation with CNC
CNC machines are gradually replacing traditional machine tools in modern industry. Longer production times are a result of manual work, but this also increases the chance of manufacturing problems. What do we gain by deciding to use CNC technology?
Precision
Unlike machines controlled manually by an operator, automatically controlled machines are capable of making even small parts with great precision.
Repeatability
Another advantage of CNC technology over traditional manufacturing is that it makes many identical parts, which is very hard to do when the human factor is involved.
Reduce production time
Automation speeds up production processes. Machines repeat a sequence of programmed movements much faster and more accurately than a human operator. This makes it possible to produce even very complex parts on a mass scale.
Cost optimization
Another disadvantage of manual machining, due to the lack of adequate precision, is the waste of material. Automatically controlled machines not only do their job faster, but also more precisely. Consequently, fewer products are rejected as defective during quality control.
In our Quality Lab, we have a CNC machine tool – DN VC 510 – which, with its rotary tables, precision spindle, advanced cooling system and programming capabilities, has all the above advantages.
Summary
CNC technology is not a method without drawbacks. It is assumed that its implementation is profitable only when more than 100 identical parts are produced. Another requirement is to create the design in CAD software. However, when we are talking about scaling production and mass production of components, especially in the automotive industry, CNC automation is a solution that is not so much more cost-effective, as it is one that enables further development of the company.
If you want to learn more about the application of CNC technology or have decided to cooperate with us, please contact us! Below you will find contact details of our expert:
Bartłomiej Szybecki
Key Account Manager
+48 884 311 422
bartlomiej.szybecki@sgpgroup.eu
A technical drawing preparation
Our offer includes preparation of technical documentation, in accordance with current technical standards. On the basis of photos, sketches, 3D models and visualization we make:
- reconstruction of existing technical documentation,
- computer-aided drafting using CAD software,
- making drawings on request.
3D Modelling
Basing on the knowledge of our design team, we offer the production of three-dimensional models based on the documentation provided by the customer.
Completed 3D models can be useful in further design work, visualization of finished products or serve as a basis for the implementation of products on CNC machine tools. It is also possible to serially produce details for the customer on the made form.
We offer:
- injection molds for plastics:
- single-slot / multi-slot
- with sliders / without sliders
- direct injection / point injection
- multi-channel
- hot channel moulding
- moulds with multi-stage ejection
- simplified projects typical for tool shops
- complete designs
- injection molds for die casting:
- single-slot / multi-slot
- with sliders / without sliders
- ZnAl dedicated forms
Design of tooling and structural solutions and prototypes
We make complete tooling projects, for instance:
- for sheet metal forming (possibility of making the first test pieces)
- measuring and control
- for machining, i.e. machining fixtures
- usable elements – full design and implementation of the method selected by the customer:
- plastic elements made by injection moulding
- plastic elements made by blow moulding
- bent sheet metal elements
- stamped sheet metal components
- components for 3D printing
- components for casting
We offer you cooperation in designing new structural solutions or prototypes. We are able to cooperate in the implementation of projects for many industries and services.
Rework
Modification and repair of existing parts provided by you in accordance with instructions and technical documentation.
SGP Quality Lab, a modern quality assurance laboratory, was established within the Katowice Economic Zone in response to companies’ needs for modern solutions in the field of quality control of parts and components.
What is X-ray used for in serial quality control?
The DR 320kV radiographic inspection system is an industrial booth for real-time inspection. It allows inspection of a detail made by any manufacturing technology in a variety of materials without mechanical interference.
We offer an X-ray system of GE Inspection Technologies company, which provides inspection solutions based on the latest technology to ensure productivity, quality and safety.
Thanks to the X|CUBE system technology we can inspect parts on many levels, both semi-finished and finally assembled elements. We help to increase process efficiency in the automotive and metallurgical industries as well as in aviation and power industry. We offer solutions for many industries where there is a demand for quick and efficient radiographic inspection of castings made of steel, plastics, ceramics and special alloys. If you have a problem with the inspection of materials, details or failure analysis, we always offer our knowledge and many years of experience.
The X|CUBE X-ray system is also equipped with computed tomograph which allows us to find even the smallest defects in the detail.
Thanks to the large size of the working chamber we are able to select a large number of parts in a short period of time.
The use of our X-ray system X|CUBE allows us to achieve efficiency up to a thousand pieces per shift.
We invite you to cooperate with us.